点击查看产品参数和报价--丨--
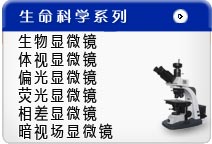
---
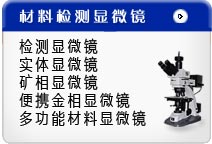
---
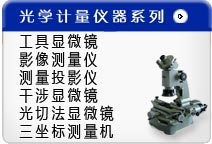
---
正文:
用自激振动使孔面得到均匀分布的波纹形微型凹坑,应对振动进行
分析,消除不利的振动,利用和调节因切削力变化所产生的自激振
动,对其进行有效控制,使切削中产生实际需要的稳态自激振动。
缸套波纹形孔面形成的工艺过程如下:
1)按波纹形孔面的要求,第一工步是在没有振纹的孔面上,镗孔
时形成原生颤振,产生振纹,为以后镗孔产生再生颤振创造条件。
因此,对第一工步镗孔前的内孔加工要求不高,留余量l一2mm,表
面
粗糙度达R。=12.5μm。第一工步镗孔后,振纹明显,振幅较
大。振纹的产生和振幅幅值的变化,往往与切削速度、刀具前角等
的选取密切相关,如图4—18所示。在同一切削速度下,当减小前
角或采用负前角时,振幅值急剧增大,反之将减小。由于本工步的
特定要求,切削中振动较强烈。为保证刀具正常切削,刀具的安装
与走刀方向形成一定的倾斜角度,在切削过程中刀刃可以适当位移
,以避免刀刃因振动而挤裂、崩碎。试验证明,采取上述措施后,
刀具在较强烈的振动情况下,还具有良好的切削性能和使用寿命。
图
振幅与切削速度的关系
2)在第一工步完成孔面原生颤振的基础上,改变刀具几何参数
和切削用量、使第二工步镗孔时出现轻度再生颤振。被镗孔表面振
纹已明显减轻,原来连接的倾斜振纹消失,产生新的振纹,初步具
备波纹形孔面的结构要求,但振幅仍较大。孔的几何精度不高,误
差较大。
3)第三、第四工步是镗孔的最后工步。为达到波纹形孔面的要
求,使用专用镗刀,采用比第二工步还低的切削用量进行加工。经
第二次再生颤振,振纹得到进一步改善,产生在螺旋方向均匀分布
的微型凹坑,形成新的波纹形孔面,同时提高了孔的几何精度,达
到工件的技术要求。
4)安排珩磨工序,去除飞边、毛刺,珩出基本光滑面,即完成
缸套波纹形孔面的全部加工。
出自http://www.bjsgyq.com/
北京显微镜百科